U.S. consumer prices increased by 3.0% in the year period ending June 30, 2023, according to the Bureau of Labor Statistics. This marked the slowest recorded rate of inflation in over two years. At that time, prices were only just beginning their historic rise caused by a combination of surging demand, crippled supply chains, and hampered production.
The headline figure was a relief to the market and Wall Street, which rose steeply on the news. The closer that the Federal Reserve comes to its goal of bringing down inflation to 2% or less without sparking a recession the more jubilant investors and businesses have become.
Despite getting closer to the Fed’s inflation goal, there are structural issues in the economy that will make getting the rest of the way to the 2% target very difficult. Chief among these will be labor costs which in the construction sector were rising faster at last measurement than at any time in recorded history.
During the first quarter of 2023, construction wages rose 5.7% year-on-year, its fastest pace since in at least the last 20 years, and one-third faster than their peak growth rate during construction’s previous boom in the mid-2000s.
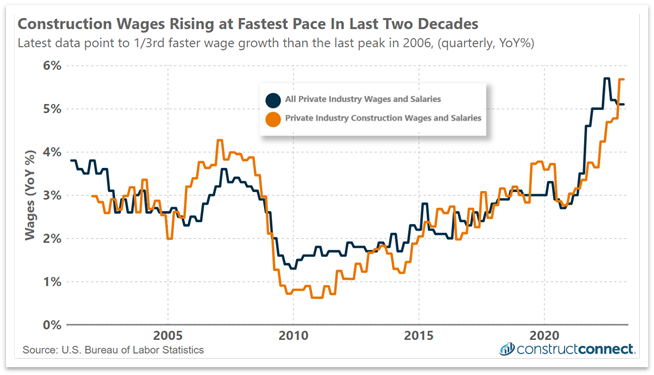
Ideally, as the Federal Reserve lowers inflation by applying just the right amount of “brake” to the economy, the demand for workers will fall, slowing wage growth. Without slowing wage growth, it will be much harder, if not impossible, to achieve long-run inflation of 2% or less. For reference, between 2002 and 2020, annual wage growth and core inflation rose by 2.5% and 1.9%, respectively.
Labor Supply Assessment
Trying to get the balance between economic growth and low inflation just right will be an upward challenge, especially in the construction industry. At the start of 2023, the Congressional Budget Office projected that the population of prime-age people (25–54-year-olds) will grow on average by 0.2% annually over the next 30 years.
That is less than a quarter of the growth rate of prime-age workers over the past 40 years (+0.9%) and hides a native-born prime-age workforce contraction that will necessitate foreign migration to sustain labor’s growth.
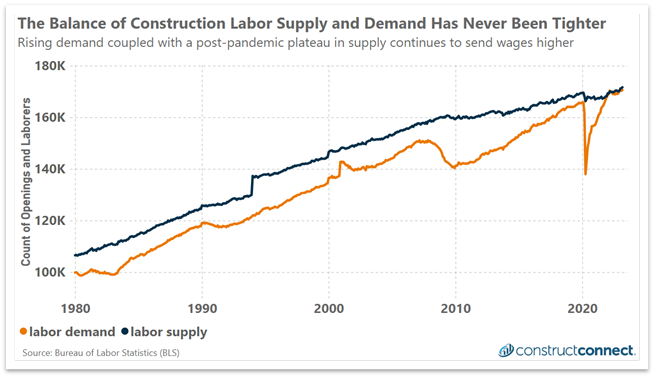
Making matters worse is a downshift in labor force participation among more experienced workers. As of May 2023, just over 38% of those 55 years old and older are working, down from over 40% pre-pandemic. The loss of these workers cannot be offset by a rise in prime-age workers which at 83.5% is already near multi-decade historic highs.

The last option for expanding the labor force is to increase the engagement of young people under the age of 25. However, cultural trends since the 1980s have seen the percentage of 16–19-year-olds working fall from a high of 58% in 1978 to 36% as of mid-2023. A similar trend is apparent for those 20-24 years old, with participation falling steadily from 80% in 1986 to 71% in the latest reading.
Labor Demand Assessment
Multiple factors will see demand for labor remain strong for decades to come. Geopolitical tensions will increase the risk of future trade disruptions, especially between North America and Asia. Such tensions have manifested themselves in various forms in the recent past, most recently in the form of a U.S. export ban on high-end computer chips.
In response to America’s move, China set retaliatory export restrictions on two essential minerals used in the U.S. to make semiconductors. A souring of trade relations may be expected to continue as the ownership of the South China Sea intensifies and especially as the Chinese government expands and strengthens its role in China’s domestic private sector.
Forwarding-looking supply chain strategists may want to consider the following statistic: If there is just a 6% chance of a significant disruption to U.S.-Asia supply chains and trade in each of the next 10 years, this would result in nearly 50-50 odds of a major disruption happening at some point during the decade. (A 6% chance of suffering a supply chain shock in any one year is 1 minus the probability of having 10 disruption-free years. 1-(0.94^10) = 0.46, or 46%.)
Such risk is almost certain to keep American companies from pursuing a return to a lowest-cost, single-source international supply chain model despite its optimized (minimized) use of labor. The potential for future disruptions to international trade between North America and Asia will necessitate a new approach to supply chains, encouraging more reshoring and near-shoring. In either situation, the demand for labor will only increase.
Furthermore, the transition to a green economy in the United States and globally will bolster overall demand for labor and especially within construction. The manufacture, installation, and maintenance of renewable energy infrastructure and electric vehicle charging stations are just two examples of industries that will require far more skilled manual labor than can be provided based on the supply constraints cited previously.
In late-2022, the Office of Energy Efficiency & Renewable Energy reported that the offshore wind turbine industry will need to increase its workforce to as many as 58,000 workers by 2024 from less than 1,000 today. This serves as just one of many examples illustrating how much additional labor is needed in the future, and before giving any consideration to other limiting factors such as job training.
How Can Businesses Prepare for the Future?
Generations of orthodox economists have accepted the now 70-year-old Solow Growth Model, which states that the growth of an economy comes down to three inputs: capital, labor, and technology. As seen in recent years, access to capital and technology remains plentiful. However, no amount of financial engineering or garage invention can fully replace the work of a man or woman 400 feet up in the air to install a wind turbine or to connect a vehicle charging station to the grid.
The recent loss of America’s most experienced workers coupled with an already highly engaged prime-age workforce has left industry leaders to fight over a pool of labor that is relatively inexperienced, relatively disengaged, and whose education is mismatched for tomorrow’s needs. Reshoring, near-shoring, and the transition to a green economy will create a prolonged fight amongst businesses for laborers that will continually push wages, and employee benefits up against the limits of what companies are able to afford.
Those businesses most likely to thrive in the coming years will be those that realize the necessity of successfully executing a labor-training, acquisition, and retainment plan, even when it results in painful consequences elsewhere in the business. Those firms that fall short of their labor growth goals will ultimately find themselves in a downward spiral as their diminishing workforce limits their ability to take on new work and opportunities.